`E005′
In an earlier post (here) we looked at the probability of occurrence of some wood products ending up out in the field … say, in buildings, having actual modulus of elasticity values equal to (as low as) the values used in stability calculations, the so-called `E min’ values. We found that, for structural glued-laminated timber (glulam), the current calculation procedure produces a modulus that is so low, … it would essentially never happen! … the probability of occurrence of such a glulam timber, is, (ridiculously) low … 1 in 3 million.
On the other hand, if we look at visually-graded sawn lumber, the same procedure for calculating Emin gives us modulus of elasticity numbers of about 1 in 200 … not what low at all! … there are sawn lumber pieces with these modulus values being installed in buildings every day.
So, you might ask, “Why don’t 1-in-200 sawn lumber pieces fail (collapse)?” … Well, this conversation is not about the probability of `collapse’, or `failure’; it’s about the probability of such a piece of lumber, or glulam timber `showing up’ at a jobsite, and being installed in a building. The question of collapse is much more robust, taking into account factors of safety, and probabilities of occurrences of the `loads and forces’, and other actions, that could cause collapse. At the end of the day, taking into account the factors of safety provided in current design practices, … way, way less that 1 in 200 sawn lumber pieces will collapse, or fail … not quite `never’, but certainly not very often. And even less often, for glulam.
So, back to 1 in 200 for sawn lumber … and 1 in 3 million for glulam. Is 1 in 200 stringent enough? Is 1 in 3 million too stringent? What if we relaxed the requirement on glulam down to 1 in 200? I am not recommending it1; I think it’s overshooting a bit, but let’s crunch some numbers through an example.
Consider a glulam timber to be used as a roof beam. The beam spans 32 feet, and is intended to carry a concentrated design load of 17,500 pounds (lb) snow load, and 3,500 lb roof dead load (roof dead weight), applied mid-span, as though from a column. (See sketch.) Plus the beam has to carry, of course, its own weight.2 It’s intended that a 6-3/4 inch-wide, 24F-1.8E glulam, manufactured from Douglas fir (DF), will be used. The design properties for this type of timber are, for modulus of elasticity, Ex = 1,800,000 psi, Ey = 1,600,000 psi, Ex min = 950,000 psi, and Ey min = 850,000 psi. (Ex and Ey shown here are `apparent’ moduli, taking into account shear deflection. These `apparent’ values are typically (more currently) identified as Ex app and Ey app.) The beam, in this example, is NOT supported `laterally’ (to resist lateral torsional buckling) along its length. The beam IS supported laterally and against rotation at the ends. Since the beam is not supported laterally, we need to look at stability (lateral torsional buckling), and, thus, `Emin’. Specifically, Ey min, will come in to play, via the Beam stability factor, CL.
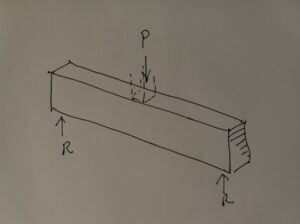
By my calculations (not shown), a 30-in. deep beam will work, using the current published Ey min value for the example 24F-1.8E beam. A beam of depth 28.5 in. (the next size shallower), will not. In both sizes, bending stress controls over others (shear, etc.), and CL controls over CV (the Volume factor). The beam size required is governed by stability, … thus Emin. The value for CL for the 30-in. depth is calculated to be 0.78. (The theoretical bending strength of the beam is reduced 22 percent to avoid buckling / lateral torsional buckling.)
Now, instead of using a `1-in-3-million’ modulus of elasticity(as provided for the 24F-1.8E beam, to address stability, let’s use a `1-in-200’ value, call it `Ey 1-in-200’ … or `Ey 005’.
First, we need to get the published Ey into a `true’ modulus, by taking out the increase due to shear deflection.
For glulam, Ey true = Ey x 1.05, or
Ey true = 1,600,00 psi x 1.05 = 1,680,000 psi ( … could round to 1,700,000 psi).
The Z statistic (assuming normal distribution) for 1 in 200 is -2.576. Using a Z of -2.576 to calculate a 1-in-200 modulus, we get,
Ey `1-in-200’ = Ey true + Z x Ey true x COVE = Ey true (1 + Z x COVE)
where
Ey true (and Ey, and E app) are `average’ modulus values,
COVE = is the coefficient of variation of modulus of elasticity, which is the standard deviation of the modulus divided by the average modulus. For glulam, COVE is taken (published) to be 0.10.
So, Ey 005 = Ey true [1 + (-2.576)(0.10)] = 1,680,000 psi (1 – 0.2576) = 1,250,000 psi (rounded a bit).
Running the design calculations with this `higher’ minimum modulus, a section 6-3/4 x 28.5 does work (1 lamination less). The corresponding CL is 0.92. But, the interesting thing (in this example), is that CL no longer controls the final outcome. It turns out that the Volume factor controls, at CV = 0.86.
Again, this doesn’t mean that 1 in 200 glulam timbers leaving the manufacturing plant and being installed … will collapse. This is 1-in-200 `occurrence’ … of being installed in a building. Design procedures addressing collapse (failure) will result in a probability of collapse… as much, much less.
In this example we were able to get to a beam with one less lamination, by relaxing modulus of elasticity used in buckling, a bit. For long, narrow beams without lateral support, we might be able to go with even lesser lams. In the above example we ran into the Volume factor controlling. In other applications deflection limitations control. Only in cases with moderately long, unsupported beams (or columns) would this reduced modulus be relevant.
1As a practicing engineer, I wouldn’t even `touch’ this 1 in 200 for glulam, unless the use of such somehow becomes `Code’.
2The calculations, `not shown’, also include beam weight.